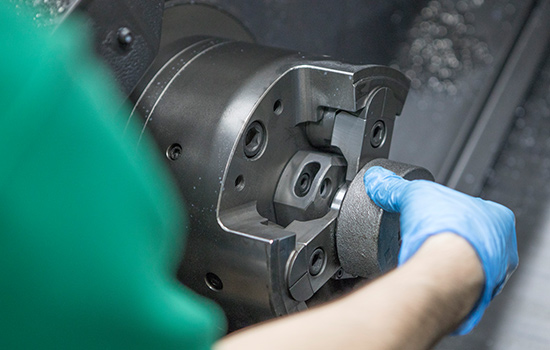
切削加工
切削加工とは、刃物(切削工具)を使用して材料を削ったり切ったりして、求めている寸法や形状に加工することです。
加工できる材料は、アルミ、ステンレス、鉄、黄銅などの金属材料の他に、プラスチックや樹脂などの非金属も材料として加工することが可能です。
切削加工の用途は、産業用機械、医療機械など、幅広い分野の部品製造に活用されており、日本の製造業を支える上で最も重要な加工技術の一つです。
ユルソンでは、自動車部品をはじめ、家電部品、農業機械等の金属部品の切削加工を行ってまいりました。
シャフト、ピンなどの円筒形状部品への溝入れ加工、ネジ切り加工など、材質は、鉄はもちろんのこと、SUS347やNSSC180などのステンレス材なども実績があります。
製造加工径:φ27~φ290 製造加工長さ:50~300
主な加工事例
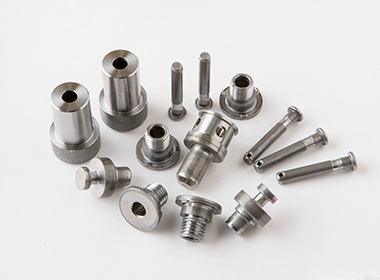
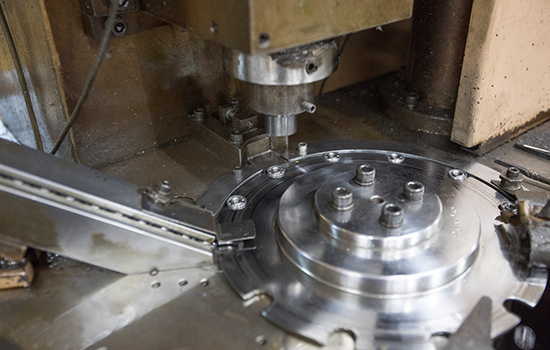
カシメ加工
塑性変形を利用して部品同士をつなぎ合わせる工法をカシメ加工といいます。部品のみで行う方法やリベットを使用する方法があり、ねじ締めや溶接とは区別される接合方法の一つです。
ユルソンでは、金属製ナットにナイロンを組み付けたり、塑性変形を利用してナットの頭頂部に変形を加えてゆるみ止め効果を発生させる、プリべリングトルク型の緩み止めナット、頭頂部をキャップ状に変形させたキャップ付きナットなど製造しております。
主に自動車部品の締結部に採用され、エンジン回りのユニットにも使用されております。
製造加工サイズ:M5~M18
主な加工事例


高周波焼き入れ加工
高周波焼き入れ加工は、高周波誘導電流を利用して鋼材の表面だけを急速に熱し、急速に冷やすことで表面を硬化させる金属処理の一つです。
鋼表面のみ硬化させて硬さを増し、内部は靭性(じんせい)を保った元の状態を保つことで、柔軟性に富んだ材料にすることができますので、耐疲労度と耐摩耗性に優れ、歯車やシャフト、平板などの機械部品の焼き入れに適しております。
ユルソンでは、専用設備により高周波焼き入れ加工を行い、自動車部品用のピンを製造しております。
主な加工事例
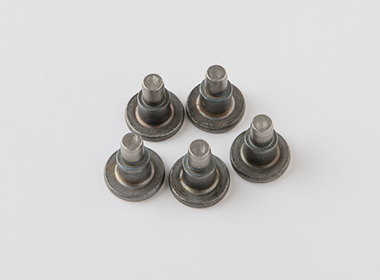
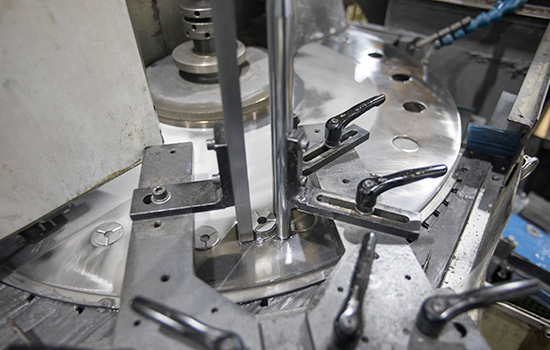
平面研削加工
金属表面の仕上げに用いられる加工方法で、砥石を用いて工作物の平面を研削加工することで工作物の厚みをミクロン単位で整え、平面度や両面の平行度を作り出します。また平面研削加工は金属だけではなく非金属であるプラスチックなどの幅広い材料に加工を施すことが可能です。
平面研削加工で使われる砥石は一つ一つの刃として作用する小さな粒の砥粒と結合剤によって形成しており、砥石の中にある気孔が切りくずの排出や冷却の手助けを行います。
高速回転する砥石の表面では刃として働く砥粒が加工物を削りながら損耗・脱落し、その下の砥粒がまた表面に出てくることで継続した研削を行います。
ユルソンでは金属材料の平面研削加工を施した自動車部品用のプレートなどを製造しております。
製造加工径:φ18~86 製造加工厚み:2.3~9.5mm
主な加工事例
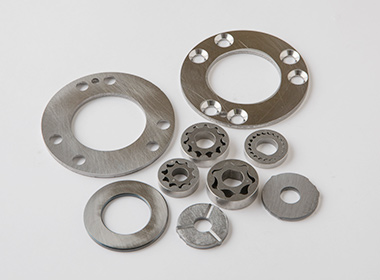
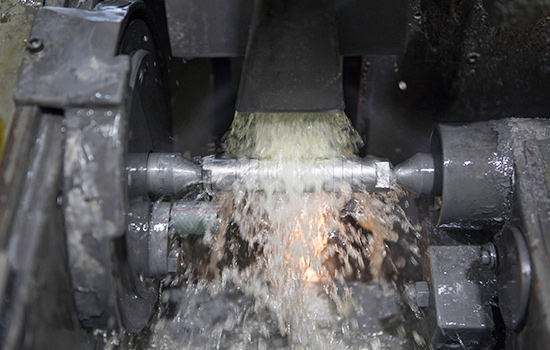
外径研削加工
円筒工作物の外周の研削を行うことを外径研削加工といいます。外径研削加工では、円筒研削盤で工作物を両センターにて支持し、補助具にて工作物を回転させ、さらに砥石を回転させながら切り込み、工作物を加工します。
仕上げ面の滑らかさはバイトで切削するものと比較にならない程のもので、表面粗さ:JIS規格の0.8S程度も容易に得ることが可能です。
寸法精度も旋盤、フライス盤よりも遙かに高精度で、焼入後の鋼鉄やクロームメッキ・超硬など硬いものも研削可能で、砥石の種類をCBN砥石やダイヤモンド砥石などを使用すればあらゆる素材を削ることが可能です。
ユルソンでは、芯無研削盤と円筒研削盤により、ミクロン単位の外径研削加工を行っております。
製造加工径:φ5.0~φ185 製造加工長さ:~90mm
主な加工事例
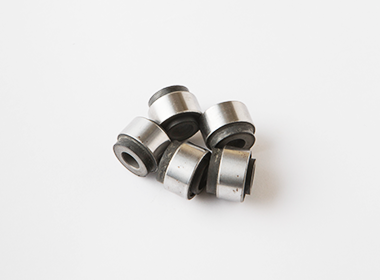
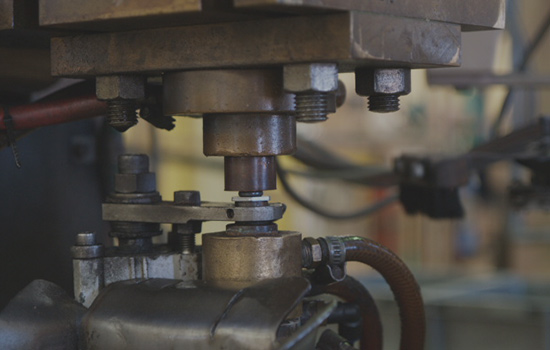
プロジェクション溶接加工
プロジェクション溶接とは、被溶接材のどちらか一方にプロジェクション(突起部)を設けて、その突起部分を加圧し、大電流を突起部に集中して流すことにより生じる発熱で、プロジェクション(突起部)を溶かし、部品同士の溶着を行う抵抗溶接の種類の一つで、平板をナットやボルトの溶接によく使われている工法です。
ユルソンでは、専用機のプロジェクション溶接機で、自動車部品の防振用プレート部品を製造しています。
製造加工ネジサイズ:M6~M8 プレート厚み:1.6~2.9 サイズ:19平~36平
主な加工事例
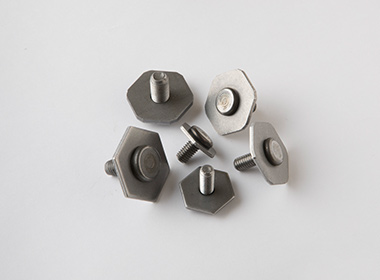
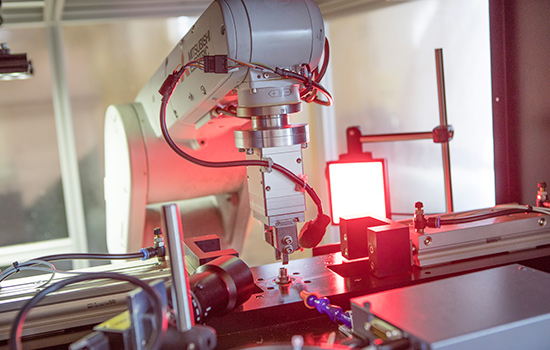
オリジナル開発
当社では、『省力化』というテーマを掲げ、ものづくりの原点を見直し、工程の効率化を実現しています。
自動車用ボルト・ピン類の切削部品加工時に切粉の巻き付きに対して目視による全数検査、また切粉除去にかかる工数を削減するための検査工程については、ロボットと検査装置からなるシステムを開発・導入し、部品ピッキング、画像処理による検査、不良品の仕分けを行うことで、検査工程の省力化、短納期化を実現し、コスト削減を図りました。
製品の開発内容は、画像処理による検査(切粉検出)のため、ロボットによるピッキングで把持したワークをカメラテーブルに搬送、テーブルを一回転し、製品の全周の画像を取得し、既存の画像処理ライブラリの機能を組み合わせ、撮影した画像から的確に切粉を検出することを可能にしました。
また、ロボットの動きを最適化することで検査時間の短縮も図りました。その結果、月間約130時間の工数削減によるコスト削減および納期短縮を達成できました。
ユルソンでは、今後も【省力化】というテーマで工程の効率化を目指し、品質・納期はもちろん、コスト競争力の向上のために、オリジナル開発を進めてまいります。
主な開発事例
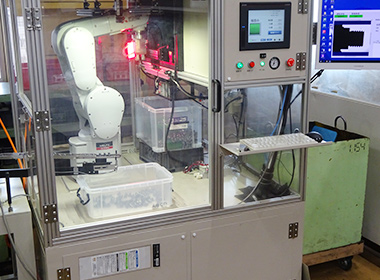